Partikelveredelung
Herstellung neuartiger funktionaler MaterialienHinter der Idee der Partikelveredelung steht der Wunsch nach verbesserten Materialeigenschaften. In der Vergangenheit hat man sich häufig auf die Herstellung immer feinerer Pulver beschränkt. Zahlreiche Anwendungen lassen sich noch weiter optimieren durch die Verwendung von Partikeln mit bestimmten Eigenschaften. Diese Eigenschaften können mechanischer, optischer, elektrischer oder auch chemischer Natur sein. Insbesondere auf den Gebieten Pharmazie, Kosmetik, Metallurgie, der Batterie-/Akkumulatorenherstellung und bei der Entwicklung von Brennstoffzellen haben sich neue interessante Möglichkeiten eröffnet. Hierbei werden Aspekte des Handlings der extrem feinen Produkte berücksichtigt. Die Grundoperationen Zerkleinern, Dispergieren, Runden, Coatieren und Agglomerieren können bei geeignetem Maschinendesign auch im Nanomaßstab angewendet werden, um die erwünschten Produkteigenschaften zu erzielen.
Partikeldesign: Technologien
- Coatieren: Feine Partikel werden durch einen mechanischen Prozess ohne Bindemittel bleibend auf der Oberfläche des Trägermaterials gebunden: Mechano-Fusion. Systeme: AMS, Nobilta.
- Dispergieren, Mikromischen: Optimale Mischgüte vom Micro- bis zum Nano-Maßstab. Systeme: Nobilta.
- Runden: Partikeldesign für bessere Fließeigenschaften und höhere Packungsdichte. Systeme: AMS, Faculty, Alpine Particle Rounder APR für Naturgraphit sowie die Sichtermühle Zirkoplex ZPS für synthetischen Graphit.
- Agglomerieren: Aufbaugranulation (kugelförmige Partikel mit schalenförmigem Aufbau) oder Agglomerieren von Primärkorn (himbeerartige Struktur). Verbessertes Handling, zusätzliches Coatieren. Systeme: Agglomaster.
Anwendungsbeispiele
Lithium-Cobaltat/Ruß
für wieder aufladbare Batterien (Akkumulatoren)Ruß wird durch einen Mechanofusion auf der Oberfläche des Lithium-Cobaltats gebunden. Der Prozess wird vorzugsweise mit dem System Nobilta durchgeführt. Der Ruß, der ursprünglich in Form von Agglomeraten vorliegt, wird in diesem Prozess dispergiert und legt sich in einer dünnen Schicht auf das Trägermaterial. Dadurch ergeben sich folgende positive Eigenschaften: verbesserte Leitfähigkeit der Elektroden, keine Agglomerate im Schüttgut, niedrige Viskosität der Suspension bei der Elektrodenherstellung.
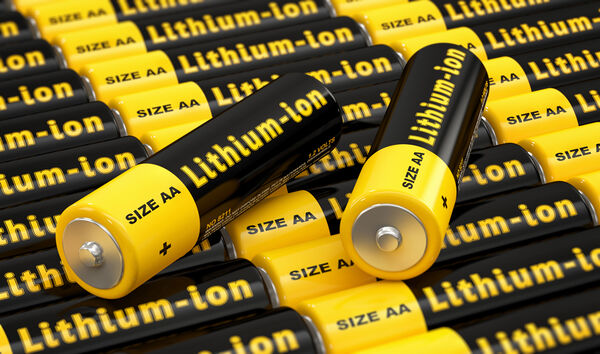
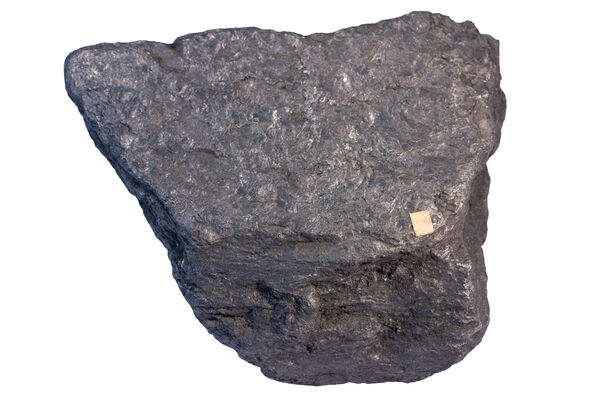
Graphit
Höhere Stampfdichte für höhere SpeicherkapazitätGraphit-Plättchen werden durch mechanische Einwirkung gerundet, gleichzeitig wird das Schüttgut entstaubt. Für diesen Prozess gibt es zwei Maschinen – je nachdem, ob synthetischer Graphit oder Naturgraphit gerundet werden soll. Bei synthetischem Graphit ist die Sichtermühle Zirkoplex ZPS die erste Wahl, für die Rundung von Naturgraphit wurde der Alpine Particle Rounder APR entwickelt. Hier wird der Naturgraphit auf einer Sichtermühle vorvermahlen. Im Anschluss erfolgt die batchweise Rundung mit nachgeschalteter Sichtung. Aufgrund der runderen Partikelform und glatteren Oberfläche ist die Stampfdichte des Materials deutlich erhöht. Die Kapazität von Batterien ist entsprechend der Stampfdichte höher.
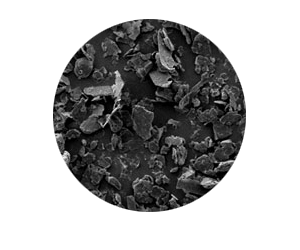
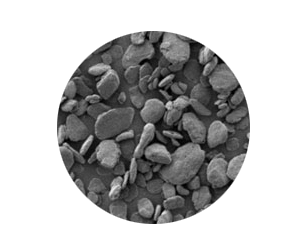
Pharmaprodukt (Trägerstoff/Wirkstoff)
Für eine gleichmäßige DosierungWirkstoffpartikel werden dispergiert und in einer dünnen Schicht mechanisch auf dem Trägerpartikel fixiert. Im Falle pharmazeutischer Wirkstoffe wird bevorzugt mit dem System AMS gearbeitet. Die Fließfähigkeit des Composits ist extrem gut und unterstützt die gleichmäßige Dosierung des Wirkstoffes. Gleichzeitig wir die Resorption des Wirkstoffes stark beschleunigt, weil der Wirkstoff auf einer sehr großen Oberfläche angeboten wird.
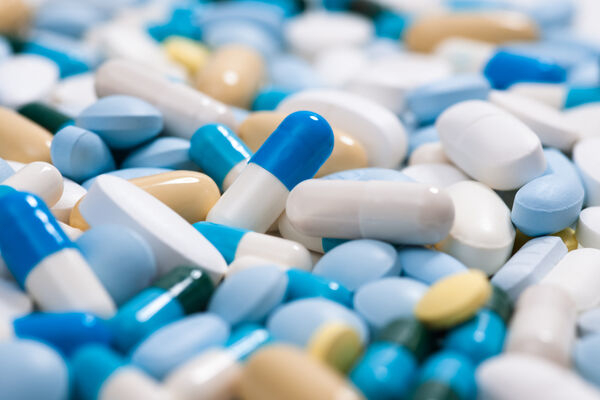
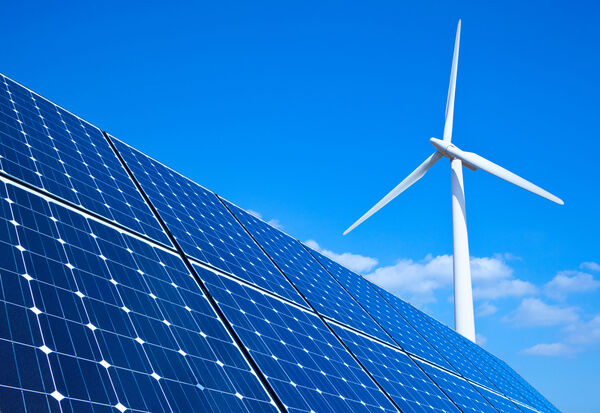
Nickeloxid/YSZ
für BrennstoffzellenNickeloxid und Yttrium-stabilisiertes Zirkonoxid (YSZ) liegen beide in feindisperser Form vor. Beide Materialien neigen stark zur Agglomeration. Bei dieser Anwendung kommt es auf eine sehr innige Verbindung der Materialien im Mikromaßstab an, wodurch die Betriebstemperatur der SOFC-Brennstoffzelle (SOFC Solid Oxide Fuel Cell) deutlich gesenkt werden kann. Die mit Abstand besten Ergebnisse werden mit dem System Nanocular erreicht, bei dem zusätzlich zu dem Mechanofusion-Prozess ein Plasma auf die Materialien einwirkt.
Mehr entdecken: Graphitrundung für Lithium-Ionen-Batterien | Alpine Particle Rounder APR | Zirkoplex ZPS